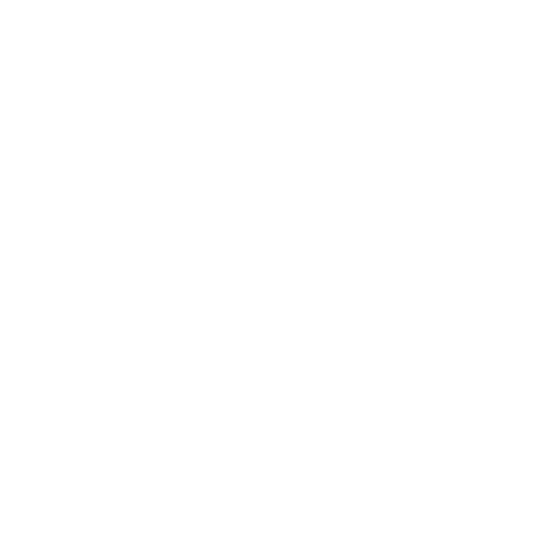
Benefits of Lean Culture
- Improved Efficiency: Processes are optimised to deliver faster and more consistent results
- Enhanced Quality: A focus on continuous improvement reduces errors and defects
- Increased Employee Engagement: Empowered teams contribute actively to organisational success
- Cost Savings: Waste elimination leads to better resource utilisation
- Customer Satisfaction: Value-driven processes ensure better service or product delivery
Key Aspects of Lean
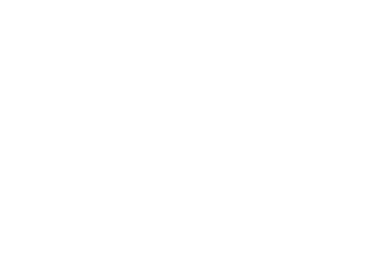
Value to the Customer
Every activity or process is evaluated based on whether it adds value from the customer’s perspective.
Efforts are streamlined to prioritise outcomes that align with customer needs.
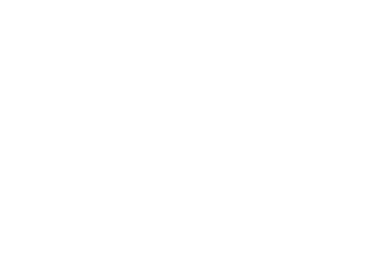
Waste Elimination (Muda)
Activities or resources that don’t contribute to customer value are identified and reduced or eliminated.
Common forms of waste include overproduction, defects, waiting times, and unnecessary motion.
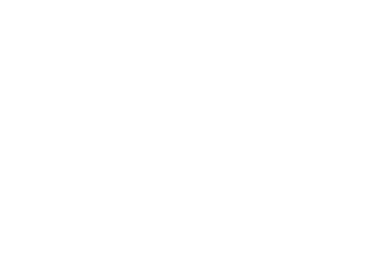
Employee Empowerment
Team members are trusted to suggest and implement improvements.
Lean culture encourages open communication and collaborative problem-solving across all organisational levels.
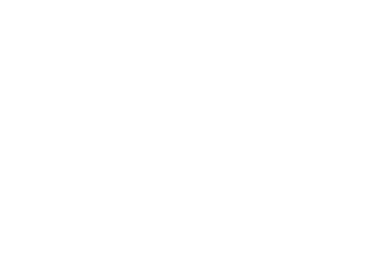
Standardisation & Flexibility
Processes are standardised to maintain quality and efficiency while remaining adaptable to change.
Continuous improvement involves refining these standards over time.
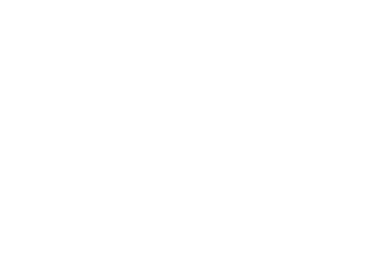
Small, Incremental Changes
Lean focuses on Kaizen, or continuous improvement through small, manageable adjustments rather than large, disruptive overhauls.
Incremental changes accumulate over time to yield significant benefits.
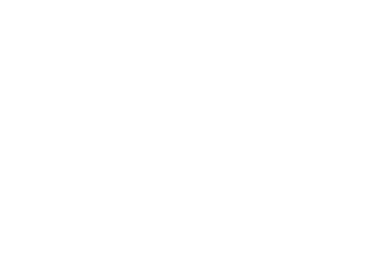
Focus on Root Causes
Problems are analysed deeply to address their root causes, rather than just treating symptoms. Tools like the “5 Whys” method are often used.
Book a Lean Tour
- Email: lean@action24.ie
- Phone: 01 297 3333
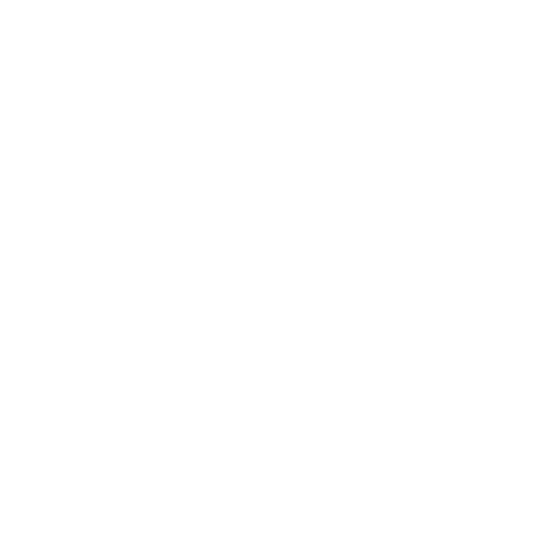
Tour Feedback
If you have completed a Lean Tour with Action24 already, we would love to hear what you think!
Please take 2 minutes of your time to fill in our feedback form!